کالیبراسیون
- 1400/08/25
- 4 دیدگاه
کالیبراسیون اندازهگیری یک کمیت و سپس تعیین صحت مقدار اندازهگیری مطابق با مرجع مورد تأیید میباشد. کالیبراسیون برای دستگاهها و وسایل اندازهگیری تعریف و تعیین میشود و برای وسیله اندازهگیری یک روش کالیبراسیون مختص به خود را دارد. بعضی از وسایل روش کالیبراسیون آنها بصورت استاندارد وجود دارد.
کالیبراسیون
در استاندارد ملی ایران کالیبراسیون (Calibration) بدین صورت تعریف میشود: مقایسه یک وسیله اندازهگیری با یک استاندارد مرجع و تعیین میزان خطای این دستگاه نسبت به آن و در صورت نیاز و لزوم تنظیم دستگاه و کالیبراسیون آن جهت مقایسه با استانداردهای مربوط به آن وسیله اندازهگیری.
به جرات میتوان گفت تمام وسایل اندازهگیری بهطور دورهای باید کالیبره شوند. علت این امر آن است که عواملی مانند گذر زمان، فرسودگی، حوادث غیرقابل پیشبینی، باعث میشود تا صحت کمیت اندازهگیری شده دقیق نباشد و نیاز به کالیبراسیون باشد.
کالیبراسیون به روشهای زیر قابلاجرا میباشد:
1- اندازهگیری و به دست آوردن خطا و ثبت نتایج
2- روش فوق را شامل میشود و علاوه بر آن، تنظیم مجدد، تعمیر و درنهایت حذف خطای ایجاد شده را به دنبال خواهد داشت.
3- این روش، روش اول و دوم فوق را شامل شده و همچنین نتایج اندازهگیری را با استاندارد مرجع و مورد تأیید مقایسه میکند و در آخر، وضعیت دستگاه از جهت قبول یا رد آن تعیین میشود.
معمولا استانداردهای کالیبراسیون به یک استاندارد جهانی که توسط سازمان استاندارد جهانی قابل ردیابی باشد ارجاع داده میشود. در علم فیزیک بحث اندازهگیری کمیتهای مختلف توسط ابزارهای مختلف همیشه مطرح میباشد، لذا تعیین روش مناسب برای اندازهگیری هر کمیت و اصلاح خطاهای موجود در وسیله تحت اندازهگیری امری ضروری میباشد. تعریف رسمی کالیبراسیون توسط ادارهی بینالمللی وزن و اندازه (BIPM: International Bureau of Weights and Measures) به این صورت میباشد: “عملی که تحت شرایط خاص در قدم نخست رابطهای بین مقادیر کمیتها با عدم قطعیت اندازهگیری برقرار میکند که این امر توسط استانداردهای اندازهگیری فراهم میشود. سپس در قدم دوم از این اطلاعات برای برقرار کردن یک رابطه برای حصول نتیجه اندازهگیری یک رویداد استفاده میکند.” از این تعریف مشخص میباشد که فرآیند کالیبراسیون به شکل مقایسه میباشد اما میتواند جنبههایی از عدم قطعیت در اندازهگیری را در رابطه با دقت ابزارهای تحت بررسی نیز معرفی کند.
هرم کالیبراسیون
هرم کالیبراسیون درواقع ساختار اجرایی و فنی عملیات کالیبراسیون را به صورت سلسله مراتبی بیان میکند. در این هرم، سیستم یکای اندازهگیری SI در رأس هرم قرار میگیرد. علت این موضوع آن است که پایه و اساس هر نوع اندازهگیری، استاندارد و یکای آن میباشد و بدون در نظر گرفتن یکای استاندارد، کالیبراسیون بی معنی است.
این هرم بصورت زیر میباشد:
یکای بینالمللی (SI)
سیستم SI بینالمللی بوده و بر اساس واحدهای اصلی: کیلوگرم، متر، ثانیه، آمپر، کلوین و کندلا بیان شده و بصورت کلی به ۲۲ زیرمجموعه طبقه بندی میشود.
استاندارد جهانی (NMI)
این استاندارد، استاندارد اندازهگیری میباشد که به تأیید سازمان NIST در آمریکا رسیده باشد.
استانداردهای اولیه (Primary Standards)
استانداردهای اولیه در استاندارد ISO 17025 بیان شده است. استاندارد اولیه اندازهگیری کمیت جرم: یکای اندازهگیری جرم، کیلوگرم است. یک کیلوگرم جرم یک استوانه از جنس پلاتین – ایریدیوم است که در اداره بینالمللی اوزان و مقیاسها (BIMP)پاریس نگهداری میشود.
استانداردهای ثانویه: استانداردی که مقدار و عدم قطعیت اندازهگیری آن از طریق کالیبراسیون یا مقایسه با استاندارد اولیهی همان کمیت مشخص میشود.
استانداردهای کاری (Working Standards)
استانداردی که به روال عادی برای کالیبره کردن یا بررسی سنجههای مادی، دستگاههای اندازهگیری یا مواد مرجع باکار میرود. استاندارد کاری معمولاً با استاندارد مرجع کالیبره میشود.
استاندارد مرجع (reference standard)
استانداردی که عموماً بالاترین کیفیت اندازه شناختی را در یک مکان معین یا یک سازمان معین دارد و اندازهگیریها از آن ناشی میشود. از استاندارد مرجع برای کالیبراسیون استانداردهای اندازهگیری کاری استفاده میشود
استانداردی که عموماً بالاترین کیفیت اندازه شناختی را در یک مکان معین یا یک سازمان معین دارد و اندازهگیریها از آن ناشی میشود. از استاندارد مرجع برای کالیبراسیون استانداردهای اندازهگیری کاری استفاده میشود
عملیات کالیبراسیونهای دورهای و روزانه که این کار توسط کارشناس و تکنسین آزمایشگاه صورت میگیرد.
دستورالعملها (Process Instruments)
این دستورالعملیها شامل دستورالعملهایی مرتبط با تجهیزات اندازهگیری میباشد که معمولاً در صنعت مورد استفاده قرار میگیرند.
عدم قطعیت در کالیبراسیون
عدم قطعیت در کالیبراسیون به معنی وجود شک و تردید در مورد تعیین صحت و اعتبار نتیجه است. بصورت کلی عدم قطعیت اندازهگیری اطلاعاتی درمورد کیفیت اندازهگیری بیان میکند. این نتیجه تنها یک تخمین کلی از مقدار واقعی اندازهگیری است و تنها زمانی کامل است که با گزارشی درخصوص عدم قطعیت همراه باشد. هنگامیکه مقدار کمی یک پارامتر فیزیکی اندازهگیری و گزارش میشود، نیاز است تا عدم قطعیت در مورد کیفیت نتیجه ارائه شود تا افرادی که آن را استفاده میکنند، قادر به ارزیابی قابلیت اطمینان آن وسیله باشند. بدون وجود این اطلاعات، مقادیر اندازهگیری شده را نمیتوان با یکدیگر مقایسه کرد.
کالیبراسیون سنسورها
به طور کلی همه سنسورهایی که تولید میشوند با نمونه مشابه خود یکسان نیستند و متفاوت میباشند و از این رو اطلاعات و نتایج مختلفی گزارش خواهند داد. تفاوت در طراحی سنسور یعنی اینکه دو سنسوری که کاملاً شبیه همدیگر میباشند، ولی در شرایط کاملاً یکسان خروجی و نتایج مختلفی از خود نشان دهند. خروجی و دادههای سنسورها به مرور زمان تغییر میکند و به کالیبراسیون دورهای احتیاج دارد.
مراحل کالیبراسیون دستگاهها
کالیبراسیون وسایل اندازهگیری امری بسیار حساس و زمانبر و ظریف میباشد. مراحل کالیبراسیون وسایل و تجهیزات اندازهگیری بصورت زیر میباشد:
مرحله اول: کدگذاری
در اولین قدم نیاز است وسایل اندازهگیری بصورت دقیق و بااحتیاط کدگذاری شوند. علاوه بر کدگذاری نیاز است که برای وسایل اندازهگیری شناسنامه تدارک دیده شود و در لیست جداگانه، نام وسایل به همراه کد آنها بصورت تفکیکشده ثبت گردد.
مرحله دوم: دستهبندی
بعد از مرحله اول که کدگذاری است، نیاز است تمام وسایل اندازهگیری ازنظر کالیبراسیون طبقه بندی گردند. معیارهای مختلفی جهت طبقه بندی این وسایل میتوان در نظر گرفت؛ مانند: هزینه، فاصله و دوره زمانی کالیبراسیون، پیچیدگی فرایند کالیبراسیون.
مرحله سوم: تعیین مقدار مجاز خطا
این یک انتظار طبیعی است که هرگز نمیتوان توقع و انتظار دقت و صحت بی نهایت از وسایل اندازهگیری داشت. با توجه به درجه دقت موردنیاز، همیشه مقداری خطا وجود خواهد داشت. تعیین حد مجاز خطا به عهده تکنسین و کاربر نمیباشد و این موضوع با توجه به کاربرد وسیله اندازهگیری و کمیت مورد اندازهگیری تعیین میشود.
مرحله چهارم: انتخاب کالیبره کننده
یکی از مهمترین مراحل در کالیبراسیون وسایل اندازهگیری، انتخاب مرکز یا فردی میباشد که عملیات کالیبراسیون را انجام میدهد. باید دقت شود در این مرحله با مراکز مورد اعتماد مشورت گرفت. کارشناسان دانشنامه تخصصی مهندسی ایران در مورد این موضوع میتوانند به شما راهنمایی دهند. جهت ثبت درخواست و پرسش خود از طریق ایمیل با ما در تماس باشید.
مرحله پنجم: اجرای فرایند کالیبراسیون
این مرحله بصورت عملی بوده و با اجرای فرایند کالیبراسیون، درصد و مقدار خطای وسیله تعیین میشود. بدین معنی که با رجوع به استاندارد و همچنین تجربه، وسیله تنظیم میشود. در صورت داشتن عیوبی اساسی، وسیله اندازهگیری جهت تعمیر به مراکز معتبر ارسال میشود. در پایان شرکت کالیبره کننده نیاز است گواهی این فرایند را صادر کند و بر روی وسیله برچسبی مبتنی بر کالیبره بوده دستگاه نصب میگردد.
مرحله ششم: ثبت سوابق کالیبراسیون
بعدازاین فرایند نیاز است که سوابق کالیبراسیون حفظ و نگهداری شود. این موضوع هنگامی اهمیت پیدا میکند که بازرسین مراکز مختلف جهت نظارت و بازبینی وسایل به دستگاهها مراجعه میکندد. سوابق کالیبراسیون از معتبرترین و مستندترین سوابقی است که بر صحت عملکرد دستگاه و سلامت کامل تجهیزات اشاره میکند. همچنین در صورت فروش تجهیزات، وجود این مدارک بسیار بااهمیت خواهد بود.
استانداردهای کالیبراسیون
- ISO 9004، بند 7-1-5 منابع پایش و اندازهگیری
- ISO 13485، بند 7-6 کنترل تجهیزات پایش و اندازهگیری
- ISO 14001، بند 9-1-1- پایش و اندازهگیری، تحلیل و ارزیابی عملکرد
- ISO 45001، بند 9-1-1- پایش و اندازهگیری، تحلیل و ارزیاب
جهت دریافت استانداردهای فوق، با ما تماس بگیرید.
کالیبراسیون فوری در مواقع زیر ضروری میباشد:
- هنگامیکه یک ابزار جدید ساختهشده باشد
- بعد از تعمیر و اصلاح یک ابزار
- هنگامیکه یک دورهی زمانی خاص سپریشده باشد
- هنگامیکه تحت ساعات زمانی مشخصی ابزار کارکرده باشد
- قبل و بعد از اندازهگیری بحرانی
- بعد از یک رویداد مانند تغییر ناگهانی آبوهوا یا قرار گرفتن ابزار در معرض ضربه یا آسیب فیزیکی
- هنگامیکه مشاهدات ظاهرشده سؤالبرانگیز باشند یا مشاهدات از ابزار تطابقی با ابزار جایگزین نداشته باشد
- برحسب نیاز خاص مانند آنچه سازندهی ابزار پیشنهاد میکند
فاصله زمانی بین کالیبراسیونها
عوامل زیادی بر روی فاصله زمانی مجاز بین کالیبراسیونها تأثیر میگذارد که باید آزمایشگاه، آنها را در نظر بگیرد. مهمترین این عوامل عبارتند از:
- عدم قطعیت موردنیاز یا اعلان شده آزمایشگاه
- خطر تجاوز دستگاه اندازهگیری از محدوده ماکزیمم خطای مجاز هنگام استفاده
- هزینه اقدامات اصلاحی وقتی که مشخص میشود دستگاه اندازهگیری به مدت زیادی برای کار مشخصی مناسب نبوده
- نوع دستگاه
- تمایل به فرسودگی و رانش
- توصیه سازنده
- وسعت و شدت استفاده
- شرایط محیطی (شرایط آبوهوایی، ارتعاش و غیره)
- نتایج کالیبراسیونهایی که قبلاً انجامشده
- سوابق نگهداری و تعمیر
- تعداد آزمایشگاههای متقابل با سایر استانداردهای مرجع یا دستگاههای اندازهگیری
- تعداد و کیفیت آزمایشهای میانیای که در خلال استفاده از دستگاه انجام میشود
- خطر و روش و ترتیب حملونقل
- میزان آموزش و مهارت کارکنان ارائهدهنده خدمات
دقت
میزان نزدیک بودن مقادیر اندازهگیری شده یک کمیت به یکدیگر در دفعات مختلف اندازهگیری را دقت یا Precision می گویند. دقت از مقایسه نتیجه مای بهدستآمده نسبت به یکدیگر سنجیده میشود. بدین صورت که هر چه نتایج بهدستآمده از اندازهگیری یک کمیت به هم نزدیکتر باشند، دقت آن وسیله اندازهگیری بیشتر است. درواقع هرچه انحراف معیار نتایج کمتر باشد، دقت بیشتر است.
به طور مثال شکل زیر اگر دایرههای مشکی را مقدارهای اندازهگیری شده یک کمیت در دفعات مختلف در نظر بگیریم، میبینیم که دایره مای مشکی (نتایج) نزدیک به هم هستند. درنتیجه دقت این دستگاه اندازهگیری مناسب است.
صحت
صحت یا درستی Accuracy میزان نزدیک بودن مقدار اندازهگیری شده یک کمیت به مقدار واقعی آن است.
درواقع یک دستگاه اندازهگیری زمانی درستی دارد که میانگین مقدارهای اندازهگیری شده توسط آن دستگاه در دفعات مختلف، به مقدار واقعی نزدیک باشد.
برای مثال در تصویر زیر اگر دایره آبی وسط را مقدار واقعی کمیت و دایره مای مشکی را مقدارهای اندازهگیری شده در نظر بگیریم، میبینیم که مقادیر اندازهگیری شده به مقدار واقعی نزدیک هستند. درنتیجه درستی این دستگاه اندازهگیری مناسب است.
در شکل زیر دقت و صحت در چند مثال توضیح داده شده است:
خطا
خطا یا Error اختلاف مقدار اندازهگیری شده با مقدار واقعی کمیت است.
انواع خطاها در کالیبراسیون
خطاها برحسب تأثیرگذاری بر روی نتیجه اندازهگیری به صورت زیر تقسیمبندی میشوند:
1- خطای کلی و عمده
2- خطا ازنظر منبع
3- خطا ازنظر نمایش
خطاهای عمده به سه دسته طبقه بندی میشود:
1- خطای ناشی از اشتباه: به طور مثال در جمع چندین مقدار اشتباهی صورت گیرد.
2- خطای ناشی از حواسپرتی: به طور مثال عدد 699 به صورت 966 خوانده شود.
3- خطای ناشی از استفاده ناصحیح و اشتباهی از تجهیزات به دلیل عدم آگاهی
خطا ازنظر منبع به دو دسته طبقه بندی میشوند:
1- خطای روشمند یا سامانمند (Systematic Error)
2- خطای تصادفی (Random Error)
خطاهای روشمند (Systematic Error)
خطایی است که در سراسر یک آزمایش به صورت ثابت تکرار میشود، مانند وجود رطوبت در مکان یا بالا بودن دما در طی مراحل اندازهگیری کمیت مورد نظر. در علم اندازهگیری خطای روشمند یا سامانمند به سه دسته خطای شخصی، محیطی و دستگاهی تقسیم میشود.
خطای شخصی شامل خطای درونیابی و پارلکس میباشد. این نوع خطاها را میتوان با ایجاد شرایط محیطی مناسب به حداقل مقدار ممکن رساند.
خطای پارلکس
فاصله بسیار محدودی بین صفحه مدرج وسیله اندازهگیری و عقربه وجود دارد. اگر خواندن از زاویههای مختلفی انجام شود. اعداد نتایج مختلفی گزارش خواهد شد. این نوع خطا را میتوان توسط یک آینه بر روی صفحه مدرج حذف نمود.
خطای درون یابی
هنگامی که عقربه روی علامت درجه بندی صفحه مدرج قرار نگیرد، اپراتورو به ناچار مجبور خواهد شد مقدار مشاهده شده را به صورت چشمی کسری از مقادیر درجه بندی تفسیر نماید. توانایی در تقسیمبندی بصورت چشمی بین درجات که بسیار ریز میباشد، کاملاً محدود میباشد و قطعاً با خطا همراه خواهد بود.
خطای محیطی
خطای محیطی مانند وجود رطوبت در محیط، فشار هوا، دما، گرد و غبار میباشد.
خطاهای دستگاهی
این خطا نیز مانند برگزاری نامناسب بر روی وسیله اندازهگیری، تراز نبودن دستگاه و فرسودگی میباشد.
خطاهای تصادفی یا کاتورهای یا رندوم در کالیبراسیون (Random Error)
این نوع خطا در یک فرایند اندازهگیری به صورت کاملاً رندم و پیشبینینشده ظاهر میشود. خطای تصادفی شامل جریان هوا، لرزش دست، سر و صدا در محیط. این نوع خطاها را میتوان با میانگین گرفتن یا روشهای آماری به حداقل رساند.
همچنین خطاها ازنظر نمایش به دودسته کلی خطی و غیرخطی تقسیمبندی میشوند.
خطاهای خطی
هنگامی که خروجی وسیله اندازهگیری با یک روند خطی از مقدار واقعی تفاوت داشته باشد، به آن خطای خطی گفته میشود و این خطا به دودسته زیر تقسیمبندی میشود:
1- خطای جابجایی از صفر: (Zero Shift Error) در این خطا اختلاف حد پایینی و بالایی، مقدار ایده آل بوده و تنها نقطه صفر جابجا شده است.
۲- خطای دهانه (میزان تغییرات)
خطای غیرخطی
خطای غیرخطی خطایی هستند که بیان کننده طبعیت نکردن نتایج اندازهگیری شده دستگاه از یک روند مشخص است. اگر چنین خطای وجود داشته باشد، بر روی دقت وسیله تأثیر گذاشته و یکی از پارامترهای وسیله اندازهگیری را که تکرارپذیری (repeatability) میباشد، غیرممکن میسازد. در صورت وجود چنین خطایی، دستگاه باید در مرحله اول تعمیر شود و پس از آن کالیبراسیون بر روی آن صورت گیرد.
مطالب مرتبط
برچسب ها : Calibration, Standards, دقت, صحت, عدم قطعیت, کالیبراسیون, هرم کالیبراسیون
دیدگاهتان را بنویسید
نشانی ایمیل منتشر نخواهد شد
تعداد 4 دیدگاه برای نوشته " کالیبراسیون" ارسال شده است .

مطالب جدید
- نرمافزار ETAP 24 2024 طراحی و تحلیل سیستمهای قدرت
- نرم افزار RehaCom 6.12.2 2024 توانبخشی شناختی
- نرم افزار Datamine Studio OP v3 2024 برنامهریزی و طراحی معادن روباز
- نرم افزار Aspen HYSYS 14.2 2024 شبیه سازی فرایندهای شیمیایی و پتروشیمی
- نرم افزار EZ-FRISK 8.06 2024 تحلیل و ارزیابی ریسکهای زمینلرزهای
- نرم افزار Foundation Design Suite 2024R1 طراحی و تحلیل فونداسیون
- نرم افزار Plexon Offline Sorter 2024 تحلیل دادههای عصبی
- نرم افزار IVA-2 2024 ارزیابی پیوسته دیداری شنیداری
- مجموعه کامل نرم افزارهای TWI 2024 مدیریت و تحلیل جوش
- نرم افزار Datamine Studio UG 3.3 2024 برنامهریزی معادن زیرزمینی

مطالب پربازدید
- نرمافزار ETAP 24 2024 طراحی و تحلیل سیستمهای قدرت
- دانلود کتاب هیدرولیک و پنوماتیک فستو Festo فارسی
- مشاوره رایگان انتخاب رشته کارشناسی ارشد 97
- دانلود نرم افزار کلید فولاد (Key to Steel) پرتابل
- دانلود رایگان استاندارد
- دانلود فول استاندارد ASTM بصورت رایگان
- آموزش میکروکنترلر AVR
- دانلود آنتی ویروس شورتکات (Back 2 Normal)
- کرک Deform – تست شده

مطالب تصادفی
- نرمافزار ETAP 24 2024 طراحی و تحلیل سیستمهای قدرت
- نرم افزار FRACPRO 2023 10.11 تحلیل شکستگی های هیدرولیکی و شکاف زنی
- پلاگین EasyPBC آباکوس، بارگذاری متناوب کامپوزیت ها
- سورس برنامه MetaBalls در OpenGL
- نورد لوله
- دانلود پروژه مدار ساعت با گیت منطقی
- نرم افزار Weldassistant 9.1 2024 مدیریت جوشکاری
- شبیه سازی، مدلسازی و بهینه سازی فرایندهای شیمیایی با ASPEN
- نرم افزار GPRSoft 2024 تحلیل دادههای رادار تصویری GPR
- دانلود کتاب آموزش فارسی UML
- طریقه انتخاب AVR مناسب
همکاران ما

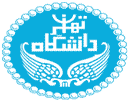
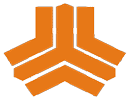
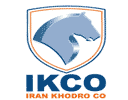
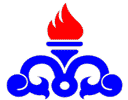


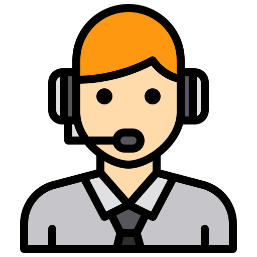
خیلی ممنون
کامل و جامع
تشکر از تیم خوبتون
تشکر
نظر لطف شماست.
مثل همیشه عالی
سپاس